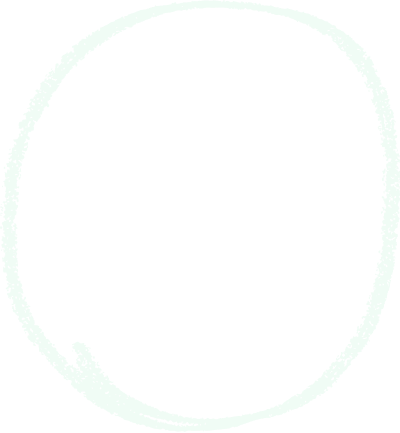
Argon Measuring Solutions & Siemens Gamesa
Working together can lead to great results. This was proven in this project where Argon, Kunlabora, and Siemens combined their expertise. Those great results may also be taken literally: Siemens is a world leader in generating power from wind turbines. They were looking for a way to assemble their wind turbines more efficiently and according to a fixed schedule.
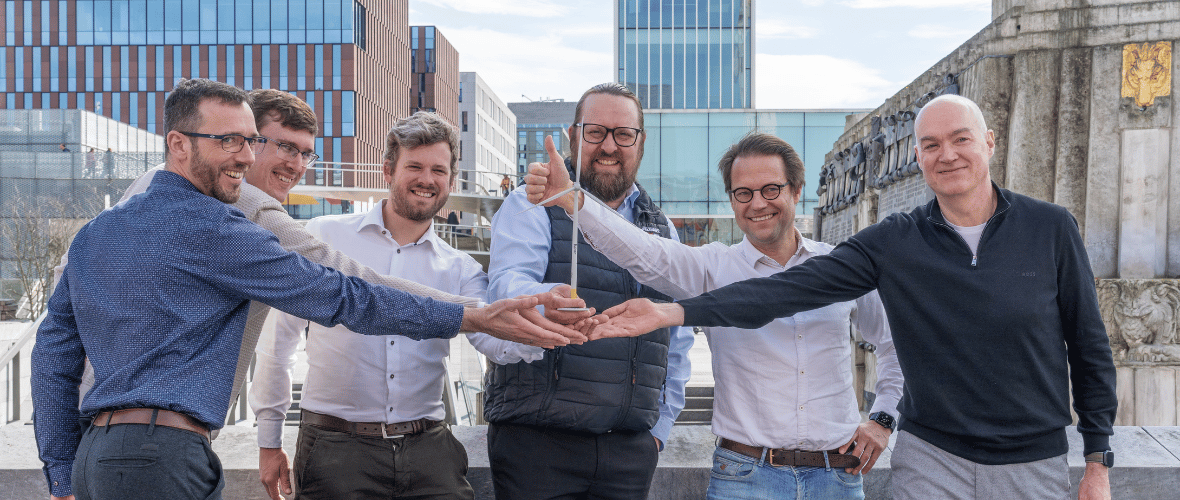
There was a high need for measuring equipment during the assembly process to achieve this goal. Enter Argon: a Belgian company specialized in 3D measuring equipment. But only measuring is not enough. Interpreting and applying the measurement data is equally essential. Enter Kunlabora. Kunlabora ensured that all measurement data are made clear to the operators in an easy-to-use dashboard.
The operation of a wind turbine in a nutshell
The wind power industry is still young and faces many challenges. On the one hand this means that there is still a lot of room for innovation, but on the other hand that it is also challenging to develop technology that does not exist yet because there is no basis of professional literature or best practices to fall back on.
In addition to being time-consuming, the production of such a turbine is a technical and complex job. In the production hall strict timetables apply. Each component of the turbine is assembled one by one per specific workstation. As a result, strict time schedules are essential.
Of course, the produced wind turbines must generate maximum energy output. The principle behind a wind turbine is fairly simple. The rotating blades of a windturbine drive the shaft of the turbine, which in turn is connected to a generator. This generator converts mechanical energy into electrical energy.
Inside the generator are rotating magnets - the rotor - and stationary copper windings, also known as the stator or coils. Due to the rotational motion of the magnets, electrical voltage is induced in the coils. To get the maximum power from the wind turbine, it is crucial that the magnets be placed as close to the coils as possible, i.e., that the rotor casing fit as closely as possible to the stator.
From innovation contest to international cooperation
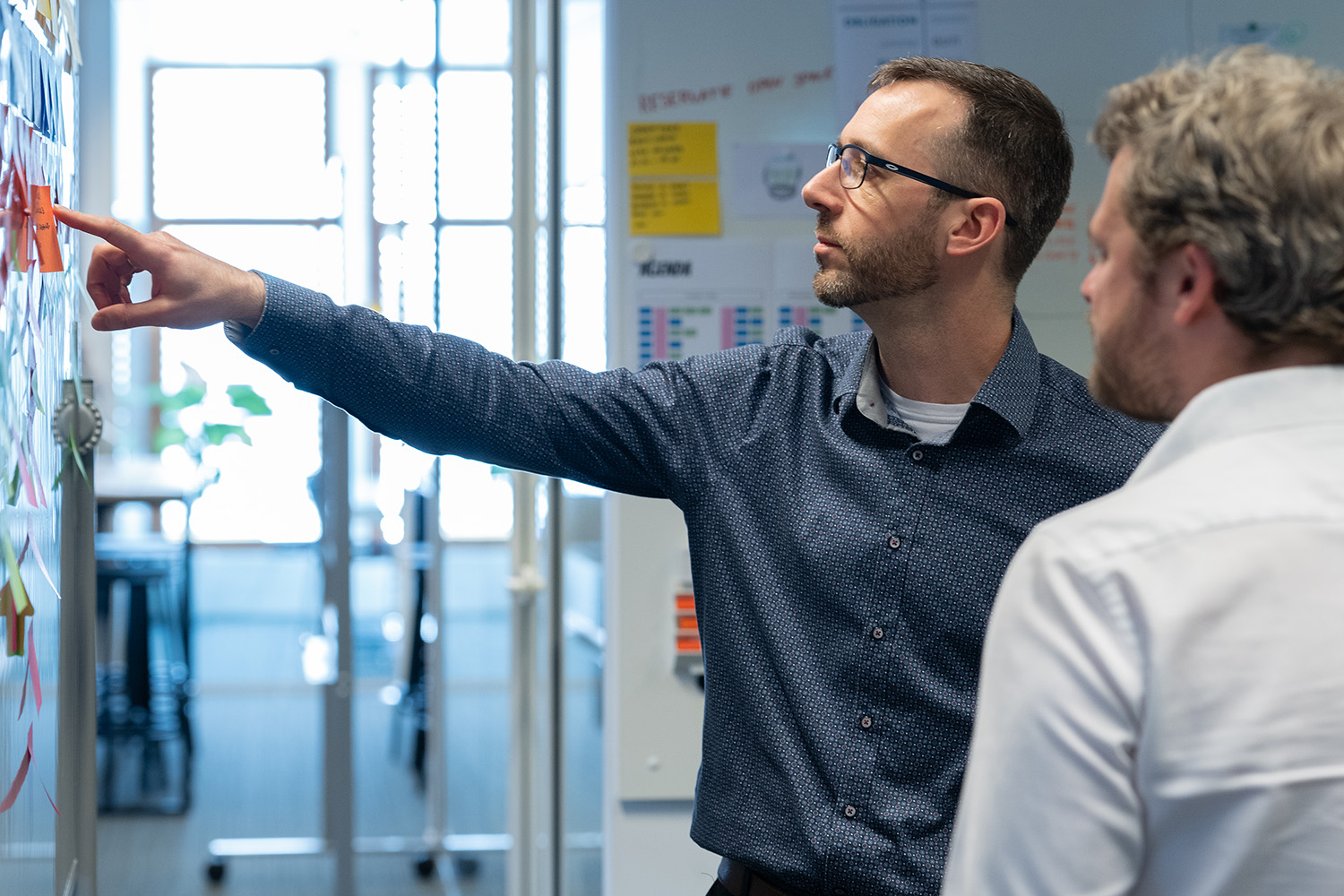
What makes the cooperation remarkable in the first place is how the collaboration came along. Siemens is strongly committed to innovation and encourages this through innovation contests in which all employees - from operators to executives - are given the opportunity to submit digitization proposals.
Two Danish employees Benjamin (production specialist) and Martin (production engineer)came up with the idea, together with their working group The Black Ninjas, to organize the production of wind turbines more efficiently by integrating measurements and data into the assembly process. The starting point of this project.
Under the old method - after the rotor was placed around the stator - pictures were taken manually all around to check if the casing was close enough to the stator. I fit was not, this had to be adjusted and the whole process repeated.
In short, the old way of doing things was inefficient, time-consuming and without a standard procedure.
That challenge was tackled by Benjamin and Martin through the introduction of measuring equipment. Through Hexagon, they met Argon: a Belgian company specialized in performing 3D measurements. Argon developed and implemented the appropriate measuring equipment to quickly perform standardized measurements in the production hall.
As an expert in Internet of Things (IoT), data analysis, and digital innovation, Kunlabora turned the measurements into an enlightening translation so that the operators in the assembly hall could interpret the generated data in an easy way.
Kunlabora, Argon and Siemens combine expertise
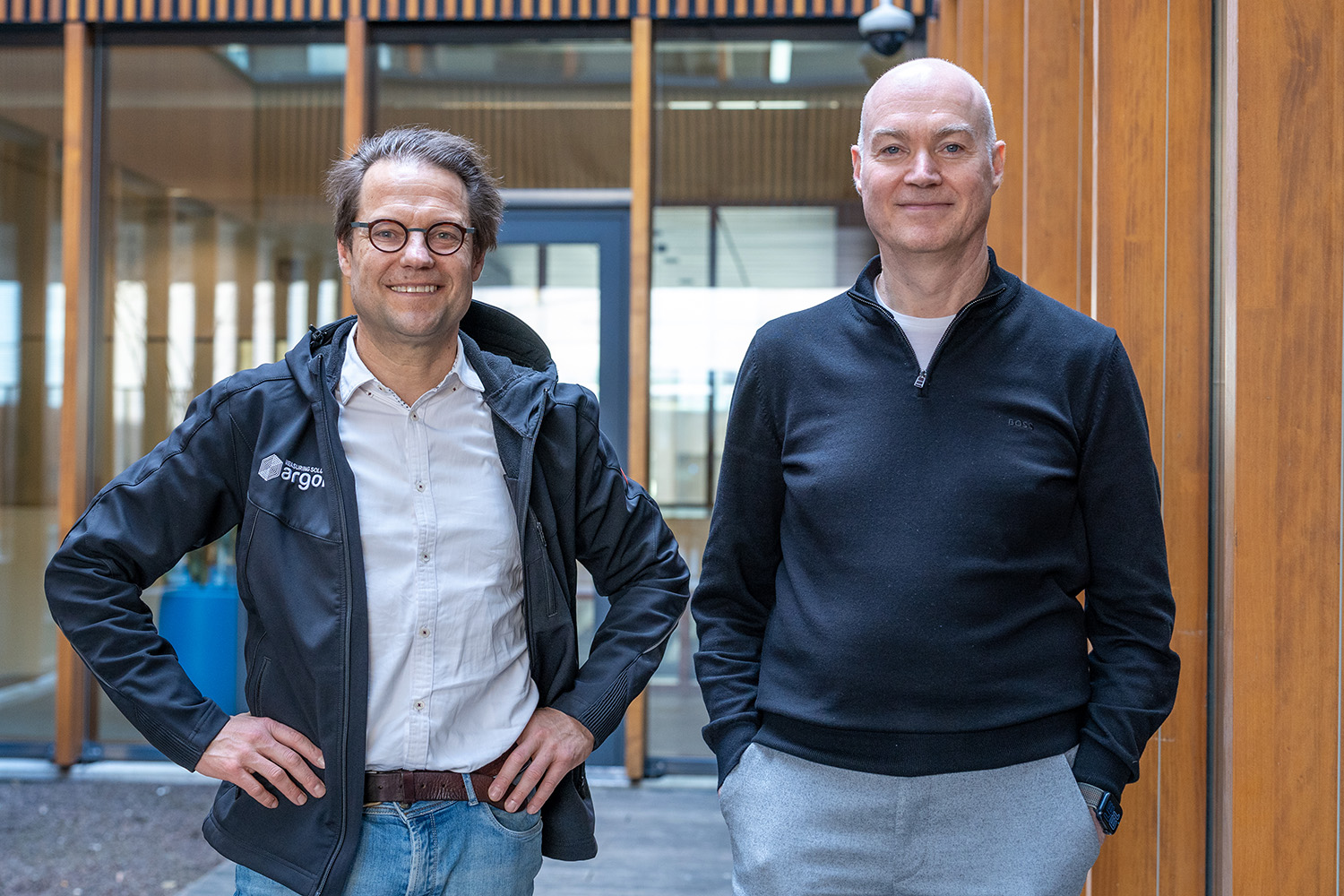
The joining of forces was necessary. With expertise in three diverse fields, knowledge and experience were combined to finish this major project successfully.
"Such a bundling of expertise in the wind industry never occurred before," Benjamin enthuses. "We were really looking for the best players in the field, because we wanted to develop something that did not yet exist. We deliberately looked for smaller partners for this purpose. Experience tells us that large players often work less agile and flexible, while we really needed out-of-the-box solutions."
The project started with a Service Blueprint by Kunlabora. An essential step given the limited lead times. Within just 2 weeks, a design, action plan and cost estimate of the project were prepared. Kunlabora developed high quality software in a short time, which could easily be expanded with additional features. At the same time, Argon developed the right set-up to perform accurate measurements.
The test setup outside the production area was necessary because production could not be interrupted and thus the technology had to be developed and tested outside the production area.
What were the biggest challenges during this project?
Big projects create big challenges. This project was no exception.
Very short execution time
The first major challenge was the incredibly short project lead time. This titanic work was accomplished in just 12 months.
On top of that, the new technology could not be tested immediately in the production area. The factory is open 24 hours a day and the production lines could not be stopped just like that. So, all technology had to be developed elsewhere and extensively tested before going into production. This added pressure: the measurement set-up had to be a first time right.
Millimeter work
As cited earlier, the casing of the rotor around the stator must fit as closely as possible to generate maximum energy. Since the equipment is worth millions,Siemens cannot afford to place both parts too closely together. It would be an absolute disaster if the two parts collided. So, the air gap between the two had to be calculated with a safety margin.
Obtaining a minimal air gap was therefore incredibly important during the project. A minimal gap means a large amount of additional energy generated by the windturbine. For the set-up, a cylinder was designed with Argon smart measurement equipment. The smart measuring instruments, which took measurements of the rotor and stator, were set up outside the generator.
Thanks to the smart measuring devices, precise measurements are now possible, so the space between the housing and the generator was made minimal.
Eventually, the maximum space was set at 5 mm. Previously, this margin stood at 8 mm. This does not seem like much of a gain, but it is: that 3 mm yields a gain of about 20% more energy production!
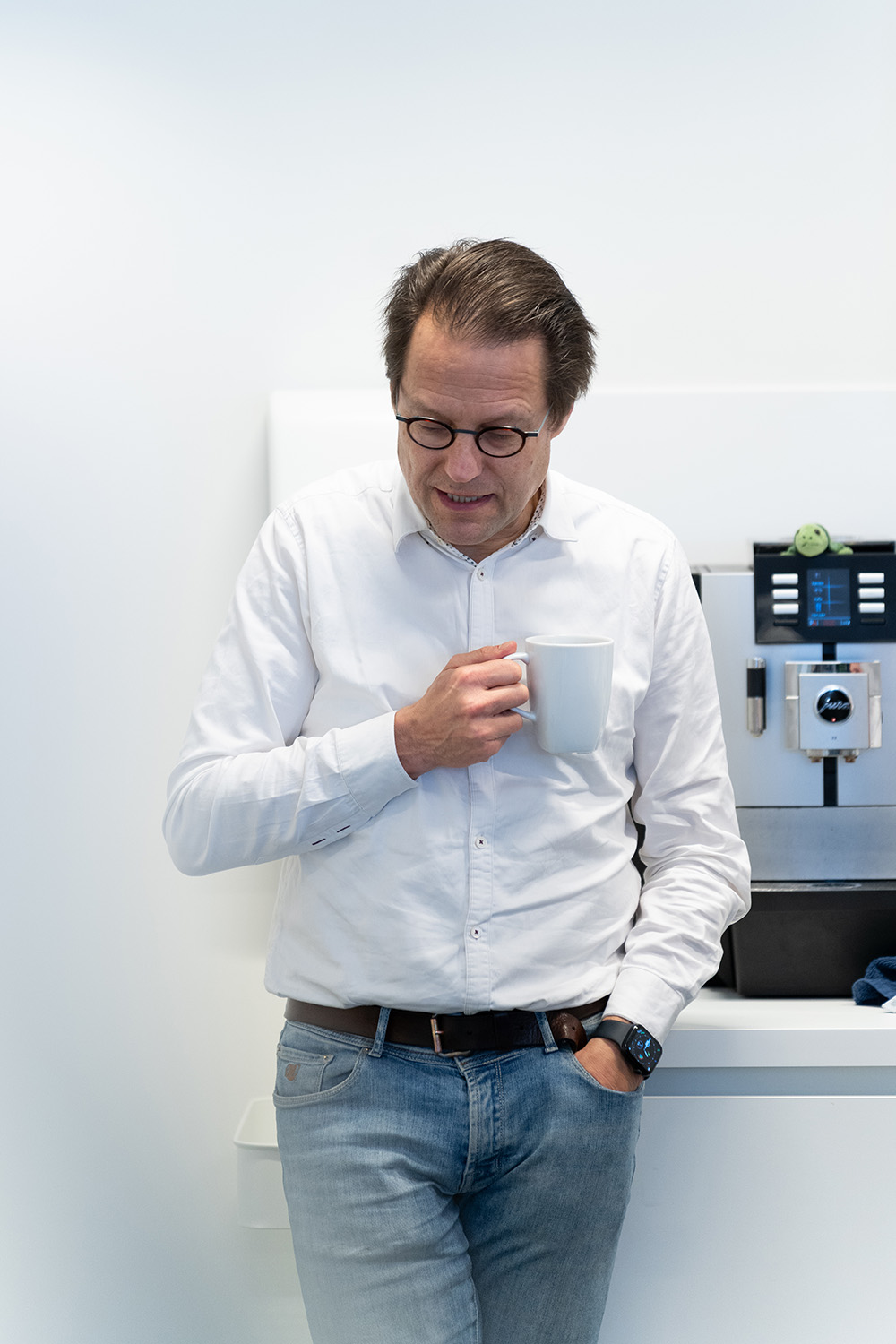
Coffee brewing principle
The new way of working, with the smart measurements and methodology, generated new challenges. Argon's smart measurement equipment produced a huge data dump.On top of that, the operators in the assembly hall are no measurement engineers. Thus, a translation of the data generated and how it reached the operators was needed.
"We don't just introduce complicated technology on the shop floor. That would be too intrusive to the way we work in the assembly room," Benjamin clarified. With this vision in mind, the working method that Argon calls the"coffee brewing principle" was introduced. Geert from Argon explains: "Everyone understands the concept of a coffee maker. So, we had to make sure that adjusting the air gap became as easy as making a cup of coffee."
Kunlabora collected all the generated data and processed it to present to the operators in an accessible way. This allows them to check, via a screen, which parts have been assembled properly and which still need adjustment.
Approved parts are highlighted in green, while parts requiring attention remain red.
Result: more power from the same wind turbines
The Siemens project team had two goals in mind. On the one hand, they wanted a standardized way of assembling wind turbines. This required data-driven decision making.On the other hand, they wanted more output per wind turbine. Or in other words: they wanted to generate more electricity.
Thanks to close cooperation, those goals were realized. First, a working method was established where stable and repeatable results were achieved per windturbine. Previously, the overall quality of a wind turbine could depend on the operator who had assembled it. This effect is now eliminated thanks to the data-driven approach.
Moreover, the maximum power output per wind turbine is achieved. During assembly, the calculation of the air gap between the outside and inside of the turbine has become less conservative. By bringing both parts closer together, the generator generates more energy. The project was a great success: the new way of working is now embraced at several Siemens production sites.
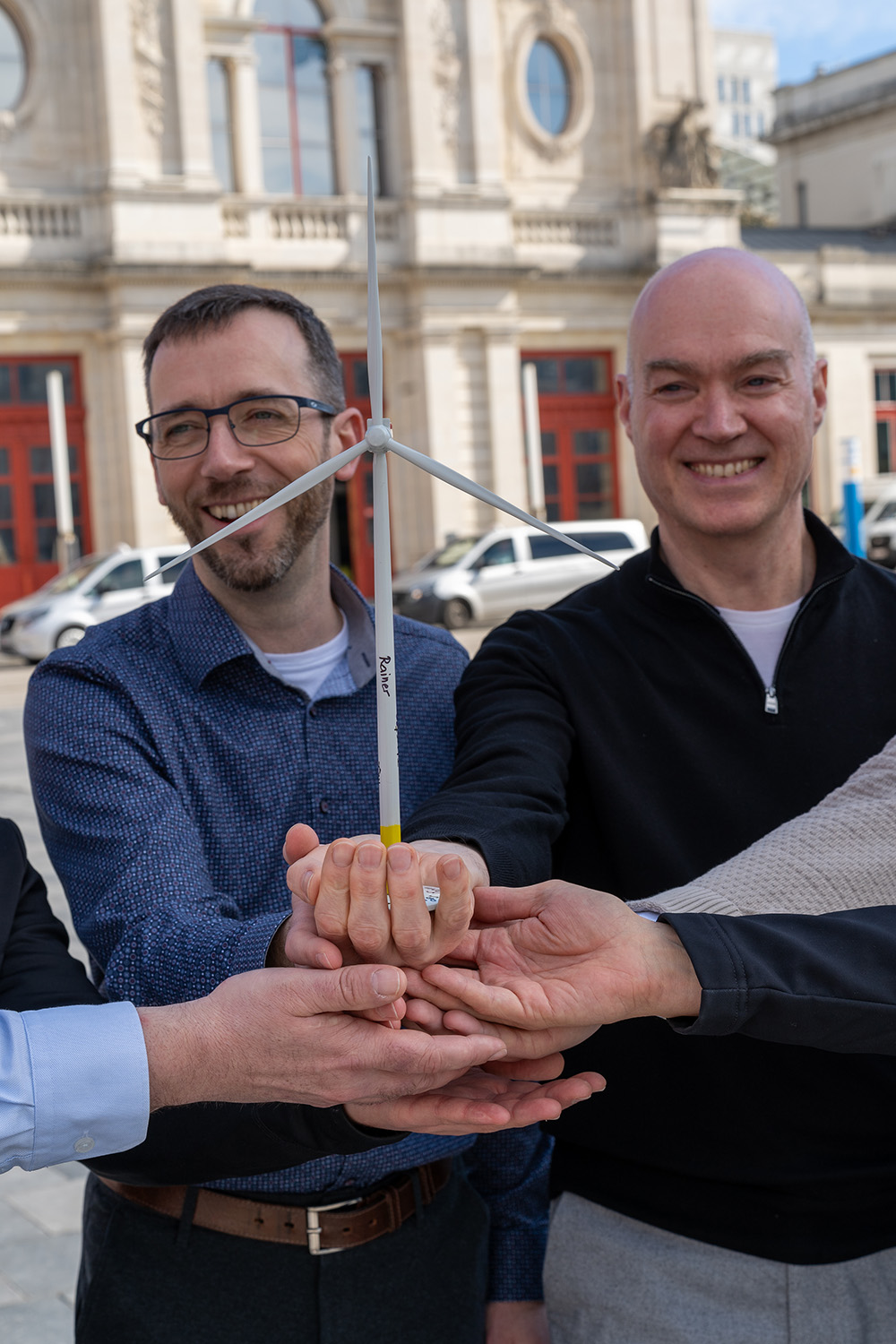
Intensive cooperation based on trust
This success story would not have been possible without the intense cooperation between Kunlabora, Argon and Siemens. But what makes this cooperation even more remarkable - was not only overcoming the geographical differences betweenDenmark, Germany, the United Kingdom, and Belgium - but also the unforeseen obstacle Covid and the fact that the three partners initially didn’t know each other.
These seem like stumbling blocks that can hinder a successful project. When asked how this was managed anyway, Martin is clear: "Trust between project partners is invaluable. Honesty, openness and sharing tons of expertise was the recipe for success of this smooth collaboration."
Steven, project manager at Siemens, underscores the power of collaboration:
"A culture of trust and communication has such a positive impact on projects, which proves the success of this story. Despite the complexity, the mentality and passion of all the partners meant a lot. It didn’t only move the projectforward, but it generates a positive impact on the planet by extension, because everyone gains by more clean energy!"
Wondering what we can do for your organization?
Inspired by this case and would you like to work together?
Contact us and we'll get back to you as soon as possible!